Safety on the job is a big concern to every worker. A workplace can be full of hazards. Slippery floors, sharp objects, moving machinery, dangerous chemicals, heavy lifting, or contaminated air are just a few examples of workplace dangers.
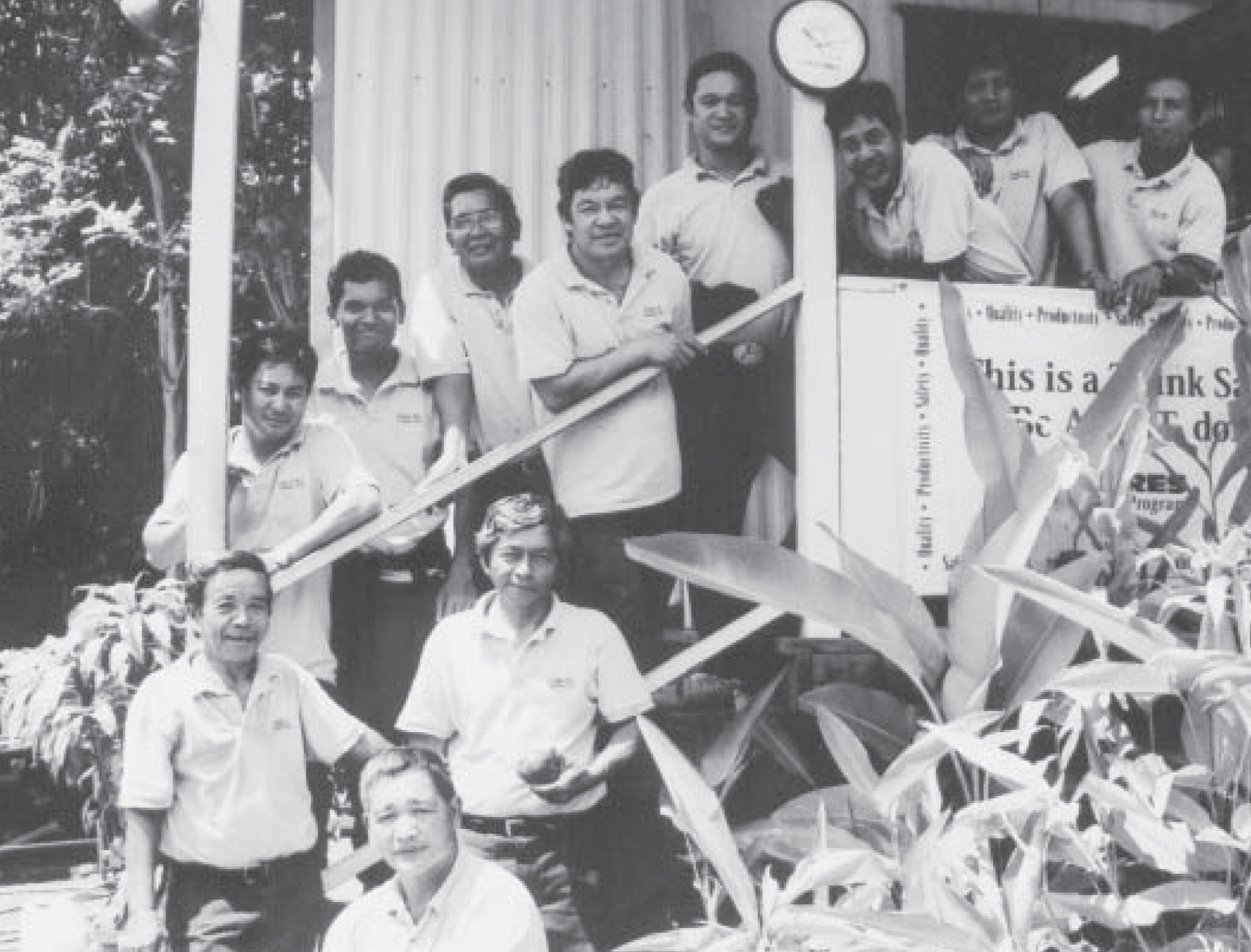
Luana Hills Golf and Country Club workers (left) need to be very conscious of job safety. Many operate heavy equipment, such as wood chippers or back hoes, while others use chemicals, like herbicides and pesticides. Work can be dangerous if not done properly, and Luana Hills employees play an important role n keeping the workplace safe and injury-free. To find our more about Unit 4421 - Luana Hills Golf and Country Club turn to pages 4 and 5.
In Hawaii, these workplace hazards killed 27 workers and injured 28,668 others in 2003, according to the latest
statistics from the state’s Workers Compensation Data Book. The actual number of injuries is much higher, as these are only the cases reported to the Hawaii State Department of Labor and Industrial Relations. No one knows how many thousands of industrial injuries and accidents go unreported.
There are several reasons why workers don’t report an accident or injury. The worker may not realize a condition is work related—this is particularly true for occupational diseases which may occur many years after an exposure to toxic substances. The worker may be too busy to take time to report an injury or may feel the injury is minor. More
importantly, many employers have counterproductive policies that discourage reporting—such as safety incentives and prizes for injury free days or drug testing people involved in accidents. These policies don’t reduce injuries—they only reduce the reporting of injuries.
Identifying hazards
The best and most effective way to reduce injuries caused by a hazard is to remove that hazard. This may sound like an obvious, common sense approach to job safety, but all too often, employers stop halfway and instead of
eliminating the hazard, they blame the worker. Employers try to change the worker with behavior based safety programs (we call these BS programs) or require workers to wear personal protective devices (PPD) such as
goggles, gloves, and ear plugs. In addition, many hazards are hidden or not easily recognized as hazards.
To identify these dangers on the job, many unions use a tool called “mapping.” In one mapping exercise, workers put colored dots on a picture of a human body, placing the dot on the part of the body that was injured. In another exercise, workers put dots on a drawing of the workplace to indicate WHERE accidents occur.
—continued on page 2
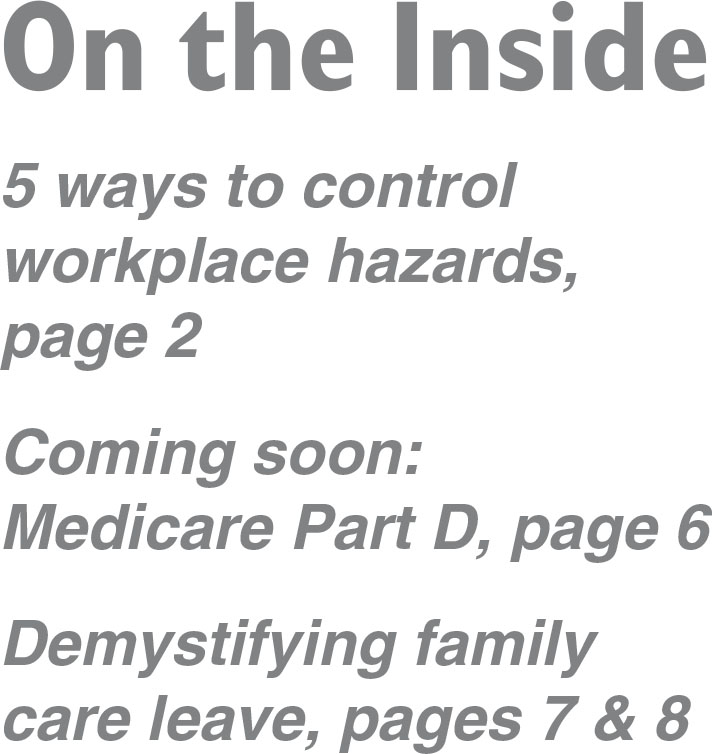
